Our rubber air spring
As a flexible elastic closed-vessel component that uses air compression elasticity to work, rubber air spring plays an irreplaceable role in automobile shock absorption, buffering, and high-frequency isolation.
To this end, after years of hard work, our company has successively developed more than 20 mature rubber air spring products such as F769, F1134445, F3027272, and S3003. The causes and solutions to some quality problems that occur during the production process of our company’s rubber air springs are briefly introduced as follows.
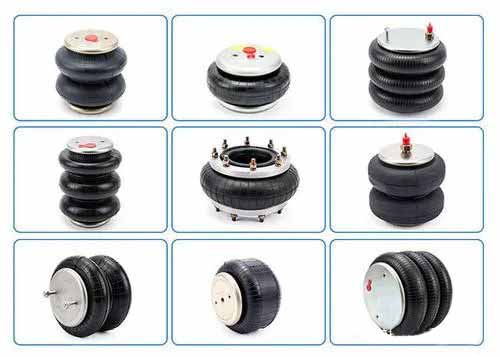
1. Rubber air spring is short of glue
main reason:
① The mold temperature is too high when loading the mold.
② The air holes in the mold are blocked, preventing the air between the rubber and the inner surface of the mold from escaping.
③ Unreasonable mold design.
④ The mold is not clean and contains dirt.
⑤ The mold (release agent) is not dry when installing the mold.
⑥ The film has poor fluidity after being parked for too long.
⑦ The vulcanization pressure is insufficient and the fluctuation is large.
solution :
① Control the mold temperature when loading the mold.
② Clear the mold exhaust holes and exhaust lines regularly.
③ Add exhaust holes for molds that are short of glue due to air pockets in concave and convex parts.
④ Clean the mold regularly.
⑤ Blow dry the mold before installing it.
⑥ The film parking time is controlled within 2-72 hours and the films are taken in the order in which they are parked.
⑦ Ensure that the vulcanization pressure meets the process requirements and remains stable.
2. Bubbles
main reason:
① There are many bubbles in the film and semi-finished products (the air spring is broken).
② During the molding operation, all the bubbles in the film and semi-finished products are not pierced.
③ The amount of return glue is large.
④ Short storage time of semi-finished products.
⑤ The mold temperature is high when loading the mold.
⑥ Insufficient vulcanization pressure.
⑦ There is dirt on the surface of the film and cord.
solution :
① Use a three-roller calendar to produce tablets, the roller temperature should be low, and the middle and lower rollers should have a small amount of accumulated glue;
② During molding, pierce all the bubbles in the film and semi-finished products, flatten and compact the semi-finished products, and drain out the air;
③ The mixing rate of return glue is controlled within 10%;
④ The storage time of semi-finished products cannot be less than 8 hours;
⑤ Reduce the molding temperature;
⑥ Control the vulcanization pressure ;
⑦ Ensure the cleanness of the film and curtain surfaces
3. Heavy skin and cracks
main reason :
① Semi-finished products, especially if there is dirt on the joint surface.
② The type of release agent is inappropriate or the application method is inappropriate.
③ The mass fraction of the release agent is too large.
④ Semi-finished products have been parked for too long, and there is dust on the surface or early vulcanization.
solution :
① Ensure that semi-finished products are clean.
② Choose a suitable release agent, such as using TSF451-1000 release agent (Japanese product) instead of silicone oil, and using a spray gun instead of a brush to spray the release agent evenly.
③ The mass fraction of the release agent is appropriate (the mass ratio of the release agent to water is 1:4).
④ Control the storage time of semi-finished products.
4. Impurities
main reason :
① The raw materials contain impurities.
② During the mixing and molding process and vulcanization and molding, impurities are mixed into the rubber material, semi-finished products, and finished products.
solution:
①Control the impurity content of raw materials.
② Filter the mixed rubber before adding sulfur. Rubber materials, films, cords, and semi-finished products must not fall to the ground. The operating sites of the mixing, calendering, molding, and vulcanization processes must be kept clean.
5. Rubber air spring capsule pleated
main reason:
① The capsule size and structure are unreasonable.
② The capsule is used for too long.
③ The capsule expands unevenly, which is obvious when using B-type capsules to produce bladder-type air springs.
solution:
①Redesign capsule size and structure.
② The capsules used should be replaced regularly.
③ Improve the tooling equipment, such as changing the outer mold for producing bladder air springs to a flexible mold to facilitate the alignment of the capsule.
6. Inflatable size exceeds standard
main reason:
① The cutting angle of the cord exceeds the standard. Since the cutting angle of air spring cords is mostly above 45°, and the company’s existing cutting machine cannot cut such cords, it can only be cut manually, so the cord cutting angle control is inaccurate.
solution :
① Make a curtain device specially used for cutting large cutting angles.
② Before measuring the cutting angle, you should first pull out the cord and pad together, and pay attention to the direction of force to avoid artificial stretching and deformation; then, separate the cord and pad, measure the cutting angle on the cord, and draw a line. Check that the angle reaches the standard before merging the curtain fabric and the cushion fabric.
③ Before forming, check the cutting angle of the cut cords one by one. Only curtains that meet the standard cutting angle can be used.
7. Conclusion
When quality problems occur in air springs, the causes must be carefully analyzed and corresponding measures taken to solve them, in order to ensure product quality, improve product qualification rates, and create good economic benefits.
Air bag rubber air spring formula
1
outer glue | |||||
Recipe 1 | Recipe 2 | ||||
Raw material name | Raw material specifications | basic recipe | Raw material name | Raw material specifications | basic recipe |
NR | 1# Smoke sheet glue | 20 | NR | 1# smoke sheet glue | 100 |
CR | 1212 | 80 | ZnO | 5 | |
ZnO | 5 | stearic acid | 4 | ||
stearic acid | 1.5 | Anti-aging agent A | 1 | ||
MgO | 3 | Anti-aging agent D | 1 | ||
Anti-aging agent A | 1 | carbon black | N774 | 40 | |
Anti-aging agent D | 1 | Channel carbon black | 10 | ||
paraffin | 1 | pine tar | 3 | ||
carbon black | N774 | 15.75 | Accelerator DM | 0.5 | |
Channel carbon black | 15.75 | Accelerator M | 0.5 | ||
rosin | 1 | sulfur | 2.85 | ||
black ointment | 2.5 | ||||
Accelerator M | 0.5 | ||||
sulfur | 1.5 | ||||
total | 149.1 | total | 167.85 |
2
Inner glue | Cord glue | ||||
Raw material name | Raw material specifications | basic recipe | Raw material name | Raw material specifications | basic recipe |
NR | 1# Smoke sheet glue | 100 | NR | 1# smoke sheet glue | 100 |
ZnO | 10 | ZnO | 25 | ||
stearic acid | 2 | stearic acid | 2 | ||
Anti-aging agent A | 1 | Anti-aging agent A | 0.75 | ||
Anti-aging agent D | 0.5 | Anti-aging agent D | 0.75 | ||
carbon black | N774 | 40 | carbon black | N774 | 15 |
pine tar | 1 | pine tar | 1.5 | ||
Accelerator M | 0.5 | Accelerator DM | 1 | ||
Accelerator TMTD | 0.05 | Accelerator TMTD | 0.04 | ||
sulfur | 2.5 | sulfur | 2.5 | ||
total | 157.55 | total | 148.54 |
3
canvas glue | Water tire rubber | ||||
Raw material name | Raw material specifications | basic recipe | Raw material name | Raw material specifications | basic recipe |
NR | 2# smoke sheet glue | 100 | NR | 2# Smoke sheet glue | 100 |
Reclaimed rubber | 40 | ZnO | 10 | ||
ZnO | 20 | stearic acid | 2 | ||
stearic acid | 2 | Anti-aging agent A | 1 | ||
Anti-aging agent A | 0.75 | Anti-aging agent D | 1 | ||
Anti-aging agent D | 0.75 | carbon black | N774 | 40 | |
carbon black | N774 | 20 | pine tar | 1.5 | |
Light calcium carbonate | 20 | Accelerator M | 0.75 | ||
clay | 20 | Accelerator TMTD | 0.03 | ||
pine tar | 3 | sulfur | 2 | ||
Accelerator DM | 0.25 | ||||
Accelerator M | 0.6 | ||||
sulfur | 2.5 | ||||
total | 229.85 | total | 158.28 |